A trailblazing windmill
How Tvindkraft got its extraordinary blades and proved that they could work
The builders of Tvindkraft accomplished more than just constructing the world’s largest modern wind turbine. They also managed to solve some major challenges in modern wind turbine design.
In the mid-1970s, there were very few examples or references available to guide the construction of a wind turbine. The windmill team in Tvind were able to find workable technical solutions that paved the way for other windmill builders and with time the wind energy industry.
The windmill team also pioneered the design of pitchable, cantilevered, fibreglass blades, which is the standard in all modern wind turbines today.
Humility and cooperation
Cooperation was key to the success of the Tvindkraft project.
Volunteers understood that they were building on old windmill traditions and that they could utilise the experience of others. They regularly consulted people with engineering experts who could assist with calculations and theories. In return, the Tvindkraft team could share how they had solved various technical issues which they had gained through hands-on experience.
As the windmill builders were happy to adopt good ideas from others, they came across their most significant technical solution, when they cooperated with friendly experts who volunteered their services.
The Tvindkraft blades revolutionised modern wind energy
To construct the long cantilevered blades, the windmill team recognised the necessity for a robust attachment point at the root of the blade. One possible solution had been demonstrated by Ulrich Hütter, a professor at the German Space Travel Institute in Stuttgart, a few decades earlier. Hütter’s innovative approach involved running continuous fibreglass strands down the blade’s length and wrapping them around the bolt holes in the mounting flange, securely attaching the flange to the blade. This attachment method became known as “the Hütter flange”. Representatives of the windmill team went to Stuttgart to learn about this technology but didn’t find a solution for the shape of the blade.
Back in Denmark, Helge Petersen from Risoe, then Denmark’s Nuclear Test Station, also offered to help. His experience was with aerodynamics and agreed to design the blades for Tvindkraft in his spare time.
The last part to be resolved was how the blades should be fastened to the hub. A solution with fibreglass strands wound around the bolts was chosen, similar to Hütter’s solution but later included a double flange and double rows of bolts.
The adapted Hütter flange and Tvindkraft’s practical adoption proved the concept worked once the turbine became operational. It was a crucial technical contribution to the development of wind turbines as we know them today.
A smaller scale windmill to copy
The windmill team building Tvindkraft also built a much smaller turbine in parallel. It was constructed using the same blade mounting technology that had been perfected on the Tvindkraft blades.
This smaller windmill was called the PTG mill. The moulds of the 4.5 m long blades were made available for other windmill builders to borrow, so they could make their own blades.
The Tvindkraft and PTG mill blade design, alongside a willingness to share the technology, were key elements that revolutionised modern wind turbine technology.
"Tvindkraft: The giant that shook the world"
“Tvind’s blade design—primarily its use of the Hütter flange—and their willingness to share the technology they had developed with other experimenters was the key element that led to what would become today’s wind industry, say Danish wind historians.”
Read Gibe & Möllerström’s article from
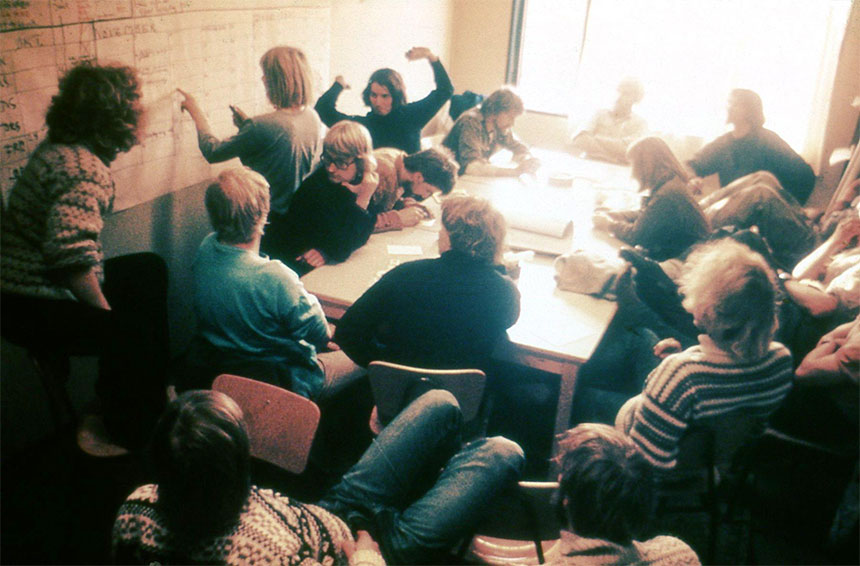
The builders of Tvindkraft accomplished more than just constructing the world’s largest modern wind turbine. They also managed to solve some major challenges in modern wind turbine design.
In the mid-1970s, there were very few examples or references available to guide the construction of a wind turbine. The windmill team in Tvind were able to find workable technical solutions that paved the way for other windmill builders and with time the wind energy industry.
The windmill team also pioneered the design of pitchable, cantilevered, fibreglass blades, which is the standard in all modern wind turbines today.
Humility and cooperation
Cooperation was key to the success of the Tvindkraft project. Volunteers understood that they were building on old windmill traditions and that they could utilise the experience of others. They regularly consulted people with engineering experts who could assist with calculations and theories. In return, the Tvindkraft team could share how they had solved various technical issues which they had gained through hands-on experience.
As the windmill builders were happy to adopt good ideas from others, they came across their most significant technical solution, when they cooperated with friendly experts who volunteered their services.
The Tvindkraft blades revolutionised modern wind energy
To construct the long cantilevered blades, the windmill team recognised the necessity for a robust attachment point at the root of the blade. One possible solution had been demonstrated by Ulrich Hütter, a professor at the German Space Travel Institute in Stuttgart, a few decades earlier. Hütter’s innovative approach involved running continuous fibreglass strands down the blade’s length and wrapping them around the bolt holes in the mounting flange, securely attaching the flange to the blade. This attachment method became known as “the Hütter flange”. Representatives of the windmill team went to Stuttgart to learn about this technology but didn’t find a solution for the shape of the blade.
Back in Denmark, Helge Petersen from Risoe, then Denmark’s Nuclear Test Station, also offered to help. His experience was with aerodynamics and agreed to design the blades for Tvindkraft in his spare time.
The last part to be resolved was how the blades should be fastened to the hub. A solution with fibreglass strands wound around the bolts was chosen, similar to Hütter’s solution but later included a double flange and double rows of bolts.
The adapted Hütter flange and Tvindkraft’s practical adoption proved the concept worked once the turbine became operational. It was a crucial technical contribution to the development of wind turbines as we know them today.
A smaller scale windmill to copy
The windmill team building Tvindkraft also built a much smaller turbine in parallel. It was constructed using the same blade mounting technology that had been perfected on the Tvindkraft blades.
This smaller windmill was called the PTG mill. The moulds of the 4.5 m long blades were made available for other windmill builders to borrow, so they could make their own blades.
The Tvindkraft and PTG mill blade design, alongside a willingness to share the technology, were key elements that revolutionised modern wind turbine technology.